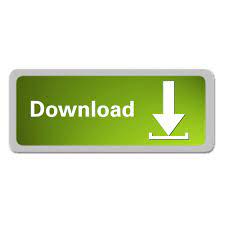

The following units are defined for use in this design example:Īdditional miscellaneous dead load (per girder):Īverage Daily Truck Traffic (Single-Lane):įor this design example, transverse stiffeners will be designed in Step 3.12.

Currently, stay-in-place forms should not be considered to provide adequate bracing to the top flange. This spacing also affects constructibility checks for stability before the deck is cured. A common rule of thumb is to make the overhang approximately 0.35 to 0.5 times the girder spacing.Ī common rule of thumb, based on previous editions of the AASHTO Specifications, is to use a maximum cross-frame spacing of 25 feet.įor this design example, a cross-frame spacing of 20 feet is used because it facilitates a reduction in the required flange thicknesses in the girder section at the pier. In addition, the overhang is set such that the positive and negative moments in the deck slab are balanced. The overhang width is generally determined such that the moments and shears in the exterior girder are similar to those in the interior girder. Further optimization of the superstructure could be achieved by revising the girder spacing.

Four girders are generally considered to be the minimum, and five girders are desirable to facilitate future redecking. For this design example, the girder spacing shown in Figure 3-2 was developed as a reasonable value for all limit states. Where depth or deflection limitations do not control the design, it is generally more cost-effective to use a wider girder spacing. Additional information is presented about the design assumptions, methodology, and criteria for the entire bridge, including the steel girder. Refer to Design Step 1 for introductory information about this design example. The girder is assumed to be composite throughout.

For this steel girder design example, a plate girder will be designed for an HL-93 live load. The steel girder design criteria are obtained from Figures 3-1 through 3-3 (shown below), from the concrete deck design example, and from the referenced articles and tables in the AASHTO LRFD Bridge Design Specifications (through 2002 interims). The first design step for a steel girder is to choose the correct design criteria.
#25 INCH MINNESOTA TEMPLATE TRIAL#
LRFD Steel Girder SuperStructure Design Example Steel Girder Design Example Design Step 3 Table of Contents Design Step 3.1 - Obtain Design Criteriaĭesign Step 3.2 - Select Trial Girder Sectionĭesign Step 3.3 - Compute Section Propertiesĭesign Step 3.4 - Compute Dead Load Effectsĭesign Step 3.5 - Compute Live Load Effectsĭesign Step 3.7 - Check Section Proportion Limitsĭesign Step 3.8 - Compute Plastic Moment Capacityĭesign Step 3.9 - Determine if Section is Compact or Noncompactĭesign Step 3.10 - Design for Flexure - Strength Limit Stateĭesign Step 3.12 - Design Transverse Intermediate Stiffenersĭesign Step 3.14 - Design for Flexure - Fatigue and Fractureĭesign Step 3.15 - Design for Flexure - Service Limit Stateĭesign Step 3.16 - Design for Flexure - Constructibility Checkĭesign Step 3.17 - Check Wind Effects on Girder Flangesĭesign Step 3.18 - Draw Schematic of Final Steel Girder Design
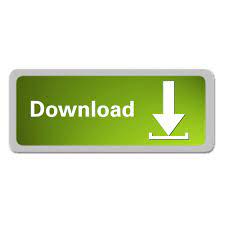